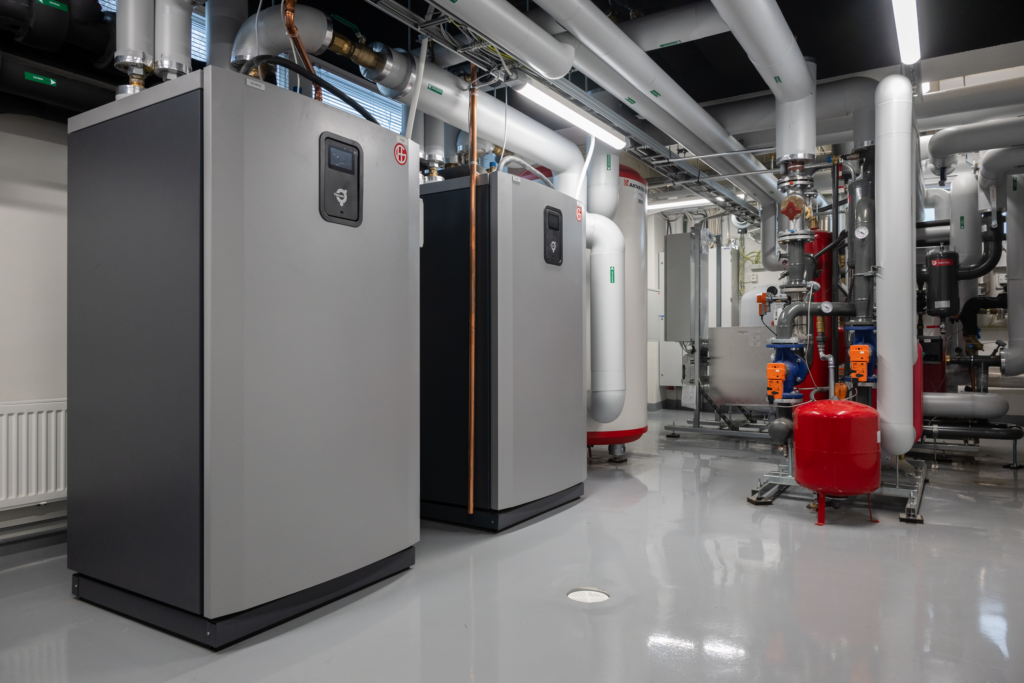
Bluefors Improved Their Energy Efficiency – Waste Heat Is Now Used for Heating
Bluefors Oy manufactures cooling and measuring equipment for developers of quantum technology. A lot of waste heat is generated in the production process of such equipment. Rejlers designed a solution that utilises waste heat for the heating of buildings and domestic water. This reduces both the need for purchased district heat and the CO2 emissions generated by heating.
Reference 3.2.2025
Project details
-
Facts
Bluefors Oy manufactures cooling and measuring equipment for quantum technology, generating significant waste heat during production. Previously, this heat was simply released into the air without being utilized.
-
What we did
Rejlers developed a turnkey solution to capture and reuse waste heat for heating buildings and domestic water. The project involved assessment, planning, contractor tendering, system commissioning, and the installation of heat pumps.
-
Highlights
The system is expected to reduce purchased district heating and emissions by 30–40% annually. Early data shows promising results, indicating that the energy-saving and emission-reduction targets will likely be met.
Previously, the waste heat generated in the production process was literally released to the sky. Bluefors wanted to build an energy recycling system that could capture and utilise waste heat for use on the property.
– We sought for a solution that would allow us to reduce the quantity of purchased thermal energy and thus achieve both monetary savings and emissions reductions. The target at the annual level was to save 30-40% in the amount of bought district heating and the emissions caused by heating, says Bluefors Facility Director Timo Palmu.
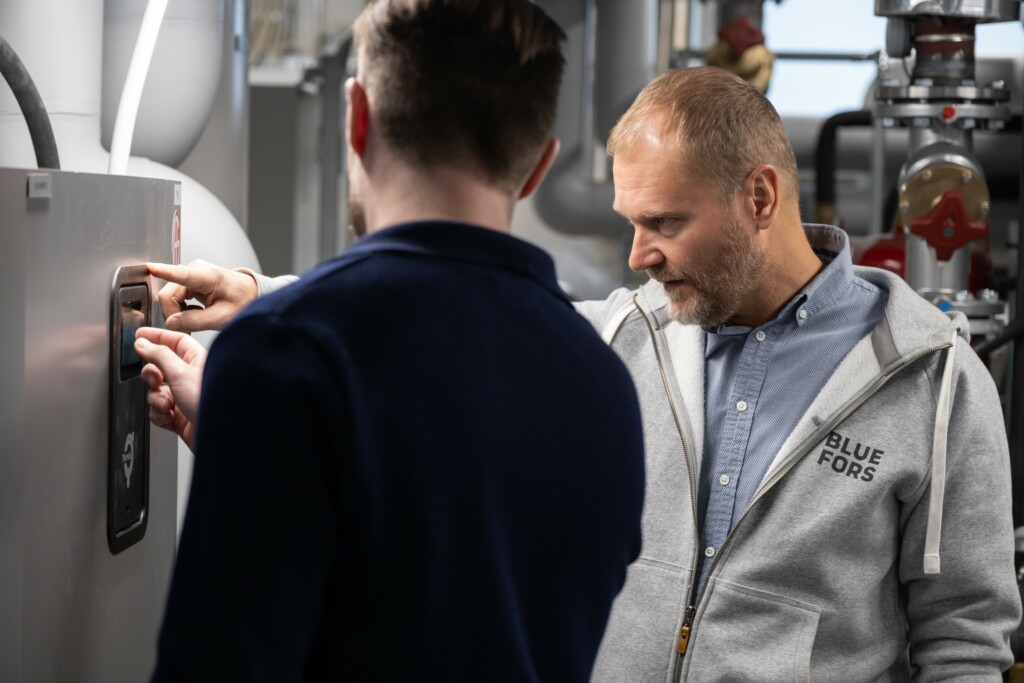
Flexible turnkey delivery by a familiar partner
Bluefors’ long-time partner Rejlers was responsible for developing the turnkey solution. The package included necessary components such as a needs assessment, an energy aid application, project and implementation planning, contractor tendering, project management, construction control, and system commissioning.
– Rejlers played a significant role, while we were mainly left with the tasks of project client. With a familiar partner and people who knew our history and production processes, the solution greatly accelerated the start-up process. This facilitated daily business and intoduced flexibility and smoothness into the project, reports Palmu.
Solution adopted in the autumn – with promising results
The outcome of the project is a system that captures the waste heat from the Bluefors production process using heat pumps and recycles it for the heating of production facilities and domestic water.
The system has been in use for a few months now. Collected data indicate that the targets set for savings and emissions reductions will be achieved.
– Initial indications are encouraging. The final results will become clear when the system has been in use for a full calendar year, but, in any case, we are clearly moving in the right direction, says Palmu.
Read more in the Bluefors blog